Las máquinas que se utilizan para la inyección de plásticos son muy específicas y tienen una serie de características y ajustes que explicaremos a continuación.
Máquinas de inyección
Las máquinas se diferencian principalmente por la ejecución de la unidad de cierre, la unidad de inyección, el accionamiento y el tipo de mando. La función de la máquina de inyección es plástificar, inyectar y moldear el plástico, así como enfriar y expulsar la pieza final.
La inyección es un proceso de transformación de plásticos en la cual se inyecta una masa plástificada a un molde. Mediante el sistema de inyección normalmente se suelen inyectar termoplásticos o termoestables.
Los termoplásticos se inyectan en un molde «frío» cuya temperatura es bastante inferior al punto de fusión de la masa. Los termoestables, por otro lado, se inyectan en un molde «caliente» para que se pueda realizar la reacción de la masa.
Desarrollo del ciclo de inyección:
- Inyección
- Postpresión
- Plastificación y dosificación
- Descompresión, apertura y expulsión
Ajuste de la unidad de cierre
Funcionamiento
La unidad de cierre soporta al molde, lo cierra, lo mantiene durante la inyección, lo abre y expulsa la pieza acabada.
Fuerza de cierre. La fuerza de cierre en las máquinas de rodillera se produce mediante una deformación elástica de la unidad de cierre al extender la rodillera; en las máquinas de accionamiento hidráulico directo se consigue la fuerza de cierre mediante la presión de aceite en el cilindro de cierre. El ajuste de la fuerza de cierre en las máquinas de rodillera se consigue mediante el aumento del recorrido de tensión y en las de cierre hidráulico mediante la elección de la presión hidráulica correspondiente. La fuerza de cierre tiene que ser tan alta que durante la inyección el molde queda cerrado, pero por otro lado tiene que ser lo más baja posible para evitar el consumo excesivo de energía, desgaste de la máquina y tener un aireado correcto del molde.
Las velocidades de cierre y apertura se pueden ajustar sin escalonamientos. Las velocidades se tienen que adaptar a los requerimientos de la pieza y del molde y por motivos de rentabilidad tienen que ser lo más alto posible.
Ajuste de la carrera de apertura. Si para desmoldear la pieza es suficiente una carrera de apertura inferior a la máxima, es aconsejable utilizar ésta para evitar pérdidas de tiempo.
Amortiguación. Para evitar un golpe brusco al abrir el molde. Se puede ajustar el comienzo de la amortiguación. Se tienen que optimizar carrera y velocidad de apertura. Un ajuste de la amortiguación para el cierre solamente es necesario en las máquinas de accionamiento hidráulico. Una amortiguación especial para cerrar las máquinas de rodillera no es necesario, ya que el final del movimiento de cierre es amortiguado por la cinemática del sistema de rodillera.
Liberación de expulsores. Al finalizar el movimiento de apertura el plato móvil puede realizar un movimiento hasta que vuelvan a desaparecer los expulsores. La liberación de expulsores sirve como ayuda de expulsión, cuando se trabaja con insertos y molestan los expulsores.
Expulsor hidráulico. Permite la expulsión de las piezas con ajuste de velocidad y de fuerza (independientemente del movimiento de apertura y de la velocidad). En el expulsor mecánico la velocidad de expulsión depende de la carrera de apertura.
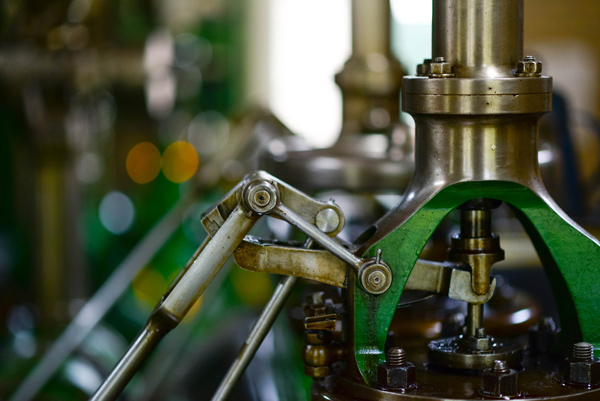
Ajuste de la unidad de inyección
Funcionamiento general
Con la unidad de inyección se plastifica la masa y se introduce en el molde situado en la unidad de cierre. La plastificación se realiza en el cilindro de inyección bajo adición de calor, mediante bandas de calefacción y por el calor generado por la fricción al girar el husillo de plastificación.
La plastificación y la dosificación están unidas entre sí. Mediante el giro del husillo se plastifica la masa y la transporta la parte delantera de ésta. Por este motivo el husillo va saliendo del cilindro. El movimiento de husillo se para cuando hay suficiente masa delante de la punta de husillo para poder llenar el molde.
Al inyectar el husillo funciona como si fuera un pistón. Mediante la presión hidráulica del cilindro de accionamiento se empuja el husillo dentro del cilindro de plastificación y presiona la masa situada en la punta a través de la boquilla al interior del molde. El husillo tiene una válvula antiretorno para evitar que la masa pueda retroceder hacia el husillo.
Con masas térmicamente sensibles (peligro de descomposición) se tiene que trabajar sin válvula antiretorno y hay que tener en cuenta una pequeña pérdida de volumen. El tipo de boquilla a elegir depende del material que se vaya a elaborar y del equipamiento de la máquina.
Tipos de boquilla
La boquilla abierta tiene las mejores condiciones de flujo de material. Con materiales muy fluidos sólo se puede utilizar cuando se hace una descompresión de masa después de la plastificación.
La boquilla abierta con rosca interior para acoplar una punta de boquilla se utiliza para:
- Acortar el bebedero
- Inyección directa sobre la pieza (sin bebedero).
La boquilla de cierre por aguja abre cuando la presión en el cilindro de plastificación, mediante el avance del husillo, alcanza un valor determinado. Se aconseja para materiales muy fluidos cuando no se puede utilizar la descompresión de masa. Con esa boquilla se evita la formación de hilos y el goteo de material, ya que la aguja cierra justo en la salida de la boquilla.
La boquilla de aguja se deja limpiar con dificultad (importante para el cambio de color y material). La boquilla de cierre por aguja con accionamiento hidráulico se abre durante la inyección hidráulicamente. De esta forma se consigue una resistencia al flujo similar a la boquilla abierta. Al dosificar se vuelve a cerrar hidráulicamente, con lo cual se vuelve a evitar la formación de hilos, goteo y gota fina igual que la boquilla de aguja.
Proceso de inyección de plástico
Las propiedades y la calidad de una pieza se determinan por el proceso de moldeo dentro del molde. Los factores que predominan son la presión y el desarrollo de temperatura dentro de la cavidad del molde. Ideal sería que la presión y la temperatura fuesen iguales en todos los puntos de la cavidad, así como el desarrollo de la presión y temperatura en el tiempo fuese de inyectada a inyectada igual. De esa forma, las contracciones, las tensiones internas y deformaciones de la pieza no existirían y todas las piezas serían igual.
Lo primero, o sea un reparto proporcional de la presión y la temperatura en el interior del molde, es al inyectar prácticamente imposible, ya que al llenarse el molde, la resistencia al flujo genera una caída de presión. También habrá diferencias de temperatura, ya que el llenado de la cavidad necesita un tiempo. De todos modos, hay que intentar acercarse lo máximo posible a la situación ideal, o sea conseguir un reparto de presiones proporcional y realizar un llenado lo más rápido posible. La resistencia al flujo durante el llenado del molde es un factor determinante: Cuanto más baja sea la resistencia al flujo, más rápido se llena el molde y por lo tanto existirán menores diferencias de presión dentro de la cavidad.
Según lo comentado, afectará en:
- El diseño de la pieza y del molde
- Los parámetros de proceso ajustables.
Presión y tiempo de inyección
La presión de inyección y de postpresión tiene que ser lo suficientemente alta para que la cavidad se llene rápida y totalmente y, por otro lado, tiene que ser lo más baja posible, para conseguir piezas sin tensiones y evitar problemas de desmoldeo.
El tiempo de inyección (tiempo de inyección y postpresión) es decir, el tiempo en el que actúa la presión de inyección tiene que ser elegido de tal forma, que dure hasta que el ataque a la pieza se solidifique. Si el tiempo de inyección es muy corto puede volver a salir masa de la cavidad y se producen rechupes y oscilaciones en las tolerancias. Tiempos demasiado largos no son rentables y aumentan las tensiones de la pieza, sobre todo en la zona de ataque. El tiempo de inyección «correcto» se puede hallar mediante el peso. Si el tiempo de inyección es mayor o igual al tiempo de enfriamiento del ataque, no suele variar el peso de la pieza. Si el tiempo de inyección es inferior al tiempo de enfriamiento del ataque, disminuye el peso de la pieza. Si salen rechupes en la pieza, es una indicación de que el tiempo de inyección es inferior al tiempo de enfriamiento del ataque.
En el manómetro de la máquina se indica la presión de accionamiento. Normalmente al elegir la presión de inyección se tiene un margen, dentro del cual a primera vista las piezas salen correctamente. El límite superior produce normalmente sobre inyectadas y dificultades en el desmoldeo, el límite inferior suele producir rechupes o un llenado insuficiente de la pieza. Este margen tenderá hacia presiones inferiores cuando se trabaja con temperaturas de masa o de molde altas.Temperatura del molde
La temperatura del molde se controla desde dos aspectos: La distribución de temperatura localmente en el molde y el comportamiento de la temperatura en el molde a lo largo del tiempo de producción.
La altura de la temperatura del molde influye en la contracción y con ello en las dimensiones posteriores de la pieza. Las diferencias locales de temperatura en el molde son determinantes para la tendencia de las piezas a la deformación. Si la temperatura del molde no se mantiene constante entre inyecciones el resultado son diferentes contracciones y variaciones en medida.
La distribución regular de temperatura en el molde depende mucho del sistema de atemperado del molde. La importancia de un atemperado suficiente y regular no se debe solamente a la influencia en la deformación de las piezas, sino también a la rentabilidad desde el punto de vista del tiempo empleado en su producción. Para el desmolden debemos esperar hasta que la zona más caliente de la pieza esté suficientemente fría. Es una premisa importante, por tanto, un atemperado intensivo y regular de todas las zonas del molde para conseguir una productividad rentable. En el caso de los noyos cuyo atemperado generalmente es complicado se producen en el momento del proyecto olvidos importantes. El molde es más barato, pero a costa de un aumento considerable del tiempo de ciclo, algunas veces hasta el 100% y más.
Para mantener una temperatura constante en el molde durante la producción se hace necesario la utilización de equipos atemperadores. Estos atemperadores deben tener una potencia acorde con los moldes donde van a ser utilizados, deben ser capaces de aportar las suficientes calorías o reducir las mismas en el tiempo adecuado.
Atemperado del molde
Al enfriarse la pieza, la temperatura es cedida al molde. Al ponerse en marcha la máquina se calienta primeramente el molde hasta la temperatura que se produce por el enfriamiento del plástico al transmitirse al molde y entorno. Esta temperatura difícilmente coincidirá con la que en la práctica se necesita para el proceso de inyección como temperatura óptima del molde. La temperatura así alcanzada se mantendrá constante solamente mientras la máquina realice un trabajo continuo, mientras no existan interrupciones en la fabricación y la relación de temperatura se mantenga constante, así como que la temperatura del ambiente tampoco varíe.
Si la temperatura deseable está por debajo de la posible con los métodos anteriores, se le debe extraer al molde la temperatura mediante refrigeración. Si la temperatura por el contrario debe ser superior a la que el molde puede conseguir por sí mismo, se lo debe aportar temperatura mediante calefacción. Se habla de atemperado fuerte cuando se extrae temperatura del molde y por atemperado flojo cuándo debemos aportar temperatura.
Debemos también prevenir contra el uso generalizado de efectuar pruebas de inyección sin tener controlada la temperatura del molde, ya que éste no está térmicamente equilibrado. Esto tendría como consecuencia no solamente el hecho de alcanzar mucho más tarde las condiciones de productividad, debido a las diferencias de medida, etc., sino que los tiempos de ciclo ajustados pueden variar también considerablemente.